Projets
Kecor
Projet lauréat du Concours i-Nov de l’ADEME : nouvelle technologie de peinture sans solvant, sans COV, pour le remplacement des peintures industrielles anti-corrosion.
Les systèmes de peintures industrielles anti corrosion classiques sont solvantés (de 20 à 70% de COV).
Appliqués en film mince, ils nécessitent plusieurs couches espacées de 24 à 48 heures pour assurer la protection anticorrosion.
Le présent projet KECOR se propose de développer une nouvelle technologie de peinture mono-composant, strictement sans solvant (COV), évitant tout rejet ou émission de CO2 dans l’environnement et qui proposera des objectifs techniques de performance inégalés. Cette technique sera d’un grand intérêt économique par rapport aux solutions existantes (gains de productivité, etc.)
-Innovation : résine mono-composant sans solvant
-Environnement : plus de rejets de COV, CO2 lors de la pose de la peinture
-Performance assurant une longue durabilité des équipements protégés.
-Sécurité et préservation de la santé des peintres/applicateurs mettant en œuvre la nouvelle technique KECOR
-Gains importants de productivité (x 3)
Le projet KECOR représente ainsi une avancée significative vers des pratiques industrielles plus écologiques et efficaces, établissant de nouvelles normes de performance, de sécurité et d’économie dans le secteur de la peinture industrielle.
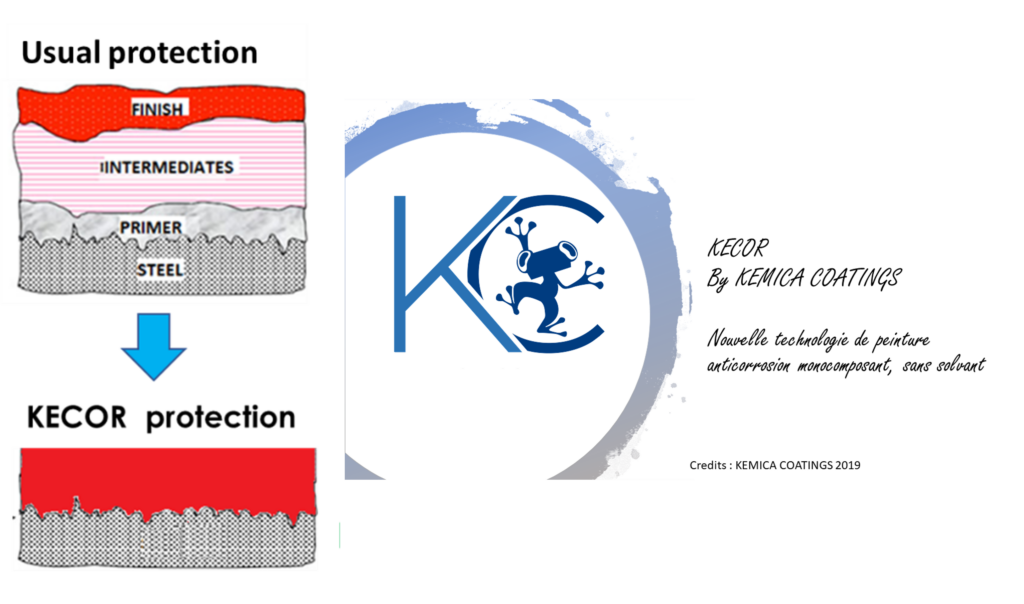
Matex
MATEX et l’effet LOTUS
Multimatériaux en Conditions Extrêmes (acronyme)
Projet en partenariat avec l’ICMN (Interfaces, Confinement, Matériaux et Nanostructures) et le GREMI (Groupe de Recherches sur l’Energétique des Milieux Ionisés) laboratoires attachés au CNRS (Université d’Orléans)
Le contexte économique recense de gros besoins en revêtements de surfaces avec des propriétés spécifiques autonettoyantes, d’antisalissure, d’antigivre ou encore d’anti-encrassement. Les revêtements dits superhydrophobes, à base de résines polyuréthane sans solvant, répondent à ces propriétés recherchées. Ils sont obtenus soit par une chimie de surface particulière (fluor, silicone), soit par une texturation spécifique des surfaces pour obtenir une topographie multi échelle (effet lotus).
La modification chimique est une voie intéressante pour les résines directement appliquées sur de grandes surfaces dans le BTP ou le Génie Civil. Par ailleurs les techniques de texturation de surface sont envisagées pour produire des membranes préfabriquées et texturées par laser/plasma, pour ensuite être collées sur chantier. Ces revêtements peuvent couvrir des éléments spécifiques comme des vannes pour les transports des gaz liquéfiés ou de pétrole afin d’assurer une protection en hiver, ou encore comme des portions de surfaces externes d’un avion ou des systèmes de raccords NABLA utilisés pour la fixation des rails de train.
Ce projet nécessite d’utiliser des additifs avec la résine pour ‘’booster’’ les propriétés de surfaces (silices fluorées, graphènes) sans utiliser de solvants. Des compétences en chimie et en physico-chimie des polymères seront sollicitées. Les techniques de texturation par plasma nécessitent également des compétences et des appareillages très pointus. En outre, il faudra penser les procédés pour qu’ils soient viable à l’échelle industrielle.
Matex
MATEX et l’effet LOTUS
Multimatériaux en Conditions Extrêmes (acronyme)
Projet en partenariat avec l’ICMN (Interfaces, Confinement, Matériaux et Nanostructures) et le GREMI (Groupe de Recherches sur l’Energétique des Milieux Ionisés) laboratoires attachés au CNRS (Université d’Orléans)
Le contexte économique recense de gros besoins en revêtements de surfaces avec des propriétés spécifiques autonettoyantes, d’antisalissure, d’antigivre ou encore d’anti-encrassement. Les revêtements dits superhydrophobes, à base de résines polyuréthane sans solvant, répondent à ces propriétés recherchées. Ils sont obtenus soit par une chimie de surface particulière (fluor, silicone), soit par une texturation spécifique des surfaces pour obtenir une topographie multi échelle (effet lotus).
La modification chimique est une voie intéressante pour les résines directement appliquées sur de grandes surfaces dans le BTP ou le Génie Civil. Par ailleurs les techniques de texturation de surface sont envisagées pour produire des membranes préfabriquées et texturées par laser/plasma, pour ensuite être collées sur chantier. Ces revêtements peuvent couvrir des éléments spécifiques comme des vannes pour les transports des gaz liquéfiés ou de pétrole afin d’assurer une protection en hiver, ou encore comme des portions de surfaces externes d’un avion ou des systèmes de raccords NABLA utilisés pour la fixation des rails de train.
Ce projet nécessite d’utiliser des additifs avec la résine pour ‘’booster’’ les propriétés de surfaces (silices fluorées, graphènes) sans utiliser de solvants. Des compétences en chimie et en physico-chimie des polymères seront sollicitées. Les techniques de texturation par plasma nécessitent également des compétences et des appareillages très pointus. En outre, il faudra penser les procédés pour qu’ils soient viable à l’échelle industrielle.
NEWSKIN
Le projet NewSkin vise à créer un banc d’essai d’innovation ouvert pour fournir à l’écosystème d’innovation les technologies, les ressources et les services nécessaires pour adopter un ensemble de processus innovants, efficaces et rentables pour fabriquer des nanotechnologies industrielles ainsi que les capacités de test nécessaires pour démontrer les caractéristiques des produits nano-améliorés.
CITEPH
«Revêtement interne des canalisations (grands et petits diamètres)». Projet sponsorisé par Subsea7, Vallourec, Saipem et Technip finalisé.
Clearsea
Nouvelle technologie de revêtement antifouling permanent et non toxique.
Le projet CLEARSEA que nous proposons de développer, concerne une nouvelle technologie antifouling qui combine le revêtement anti-corrosion et la modification de sa surface avec une finition en fibre. Il s’agit d’un système complet qui inclut :
- L’application d’une résine de protection contre la corrosion en film épais (environ 0,7 mm, l’épaisseur requise sera validée par ce projet) directement sur la coque du navire : ce revêtement est un système homogène, sans microporosité et sans aucun risque pour l’environnement (résine à deux composants, 100 % de contenu sec).
- La couche de finition CLEARSEA, qui est modifiée pour être projetée par électrostatique, sera immédiatement appliquée par pulvérisation sur la première couche de la même résine anti-corrosion et sur laquelle les fibres seront fixées par projection électrostatique. Ainsi, le revêtement de protection anticorrosion et la couche de finition CLEARSEA seront parfaitement homogènes (poids du système : environ 1,3 kg/m²), sans risque de détachement, et suivant parfaitement la géométrie du substrat. Le système est destiné à être inspecté et éventuellement renouvelé en cale sèche tous les 10 ans.
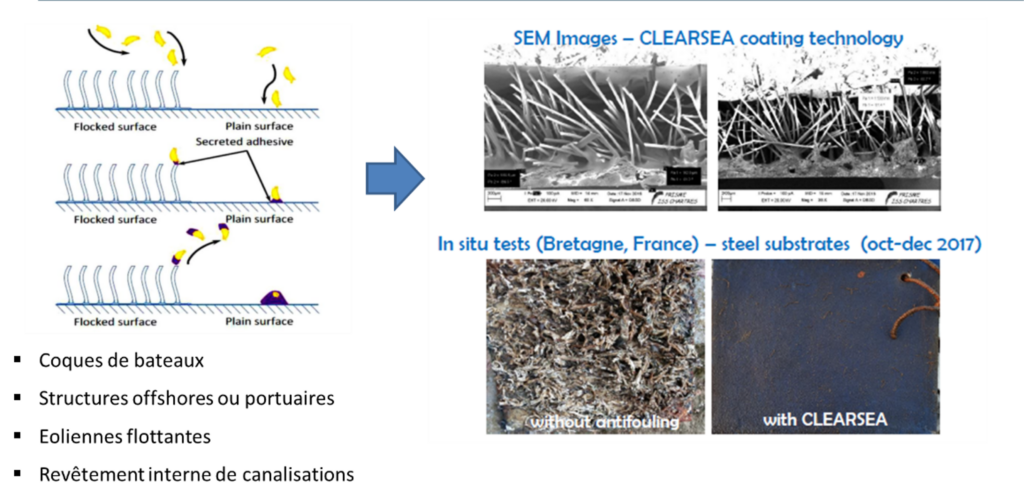
Vulcain
Candidat au dispositif d’aide ADEME France-2030 : Produits biosourcés et biotechnologies industrielles
Cet appel à projets ambitionne de développer une filière industrielle française compétitive.
Pour assurer un approvisionnement sûr et durable des matériaux de construction, il devient essentiel de rechercher des solutions complémentaires novatrices qui pourraient réduire les tensions sur le marché du bois. De nombreux industriels se mobilisent pour trouver des solutions, dans le but de répondre aux enjeux environnementaux, tout en maintenant un équilibre face à la demande croissante de ce secteur.
Les matériaux composites et biosourcés représentent une parfaite solution de substitution aux consommables non renouvelables. Le projet collaboratif VULCAIN ambitionne de développer un matériau composite innovant, durable, biosourcé et respectueux de l’environnement. Ce composite VULCAIN sera constitué d’une matrice polymère à base de polyuréthane biosourcé et d’un renfort ou charges issus des déchets végétaux, principalement de la rafle de maïs. Le composite VULCAIN permettra à la fois une valorisation au maximum du potentiel de ressources issues de la biomasse et la minimisation des déchets produits lors des constructions.
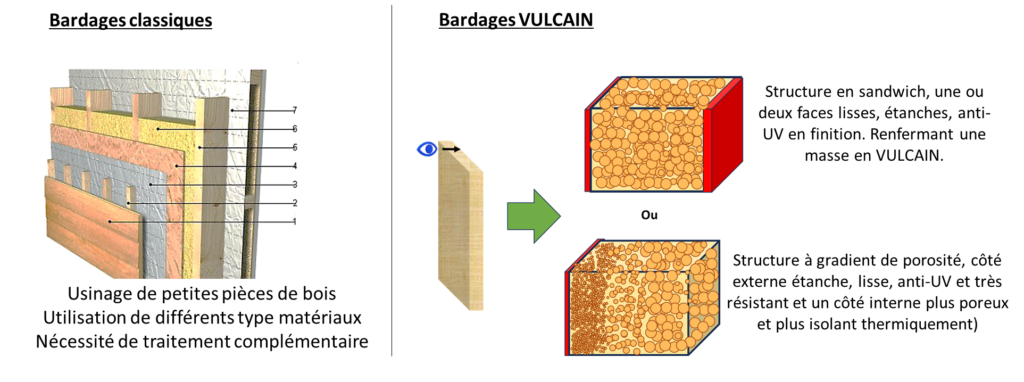
RECOUVREMENT DE L’AMIANTE
Nouvelle technologie de désamiantage par recouvrement de l’amiante avec une résine sans solvant sur un support solide
Certains matériaux contiennent des fibres d’amiante dans leur composition, destinées à améliorer leur tenue mécanique ou leur tenue au feu. Ces matériaux exposés à l’air, aux intempéries, aux risques d’incendie etc. présentent des risques de relargage de fibres d’amiante dans l’air ou dans l’eau avec les conséquences sanitaires qui en découlent. L’objet de l’innovation proposée est de bloquer les fibres d’amiante dans leur support évitant tout risque de migration ou de relargage dans le milieu environnant quelques soient les circonstances.
L’enrobage des matériaux contaminés avec une résine polyurée-uréthane sans solvant, sans odeur en une épaisseur de 1 à 2 mm permet ainsi d’inerter les supports amiantés. Les variations dimensionnelles des supports, l’exposition aux UV, etc. ne doivent pas affecter la protection des supports.
La technique de pose de la résine d’enrobage peut être applicable manuellement ou par projection mécanique.